Process Improvement

Introduction
Modern plants incorporate a complex Safety Instrumented System technology, governed by complicated standards and regulations, containing ongoing operational administrative requirements.
During the operations phase, ongoing SIS-related tasks such as compliance with those requirements, performance monitoring, maintenance, SIF bypassing, management of change, periodic proof testing, and ongoing suitability verification, require the attention, time, and effort of engineers and technicians.
The accuracy of that work is important, and yet much of it is often overlooked or accomplished using inconsistent, time-consuming, and error-prone methods. We cannot just trust that everything is going well with the SIS (Safety Instrumented System)
According to customer feedback, these tasks are many times accomplished using inconsistent, error-prone, and potentially unreliable methods such as uncontrolled spreadsheets, notes, homegrown applications, and manually marked up drawings and sketches. There is often no organized method applicable to similar SIFs at different sites.
As a result, no “single point source of the truth” exists. The many different operating and maintenance procedures referring to the SIFS may not be consistent with the SIF design. For example, an operating procedure may mention one setpoint for SIF activation, a SIF design document specifies a different one, and a maintenance test procedure in the work order generation system has another – it is common for disparate systems to accumulate errors.
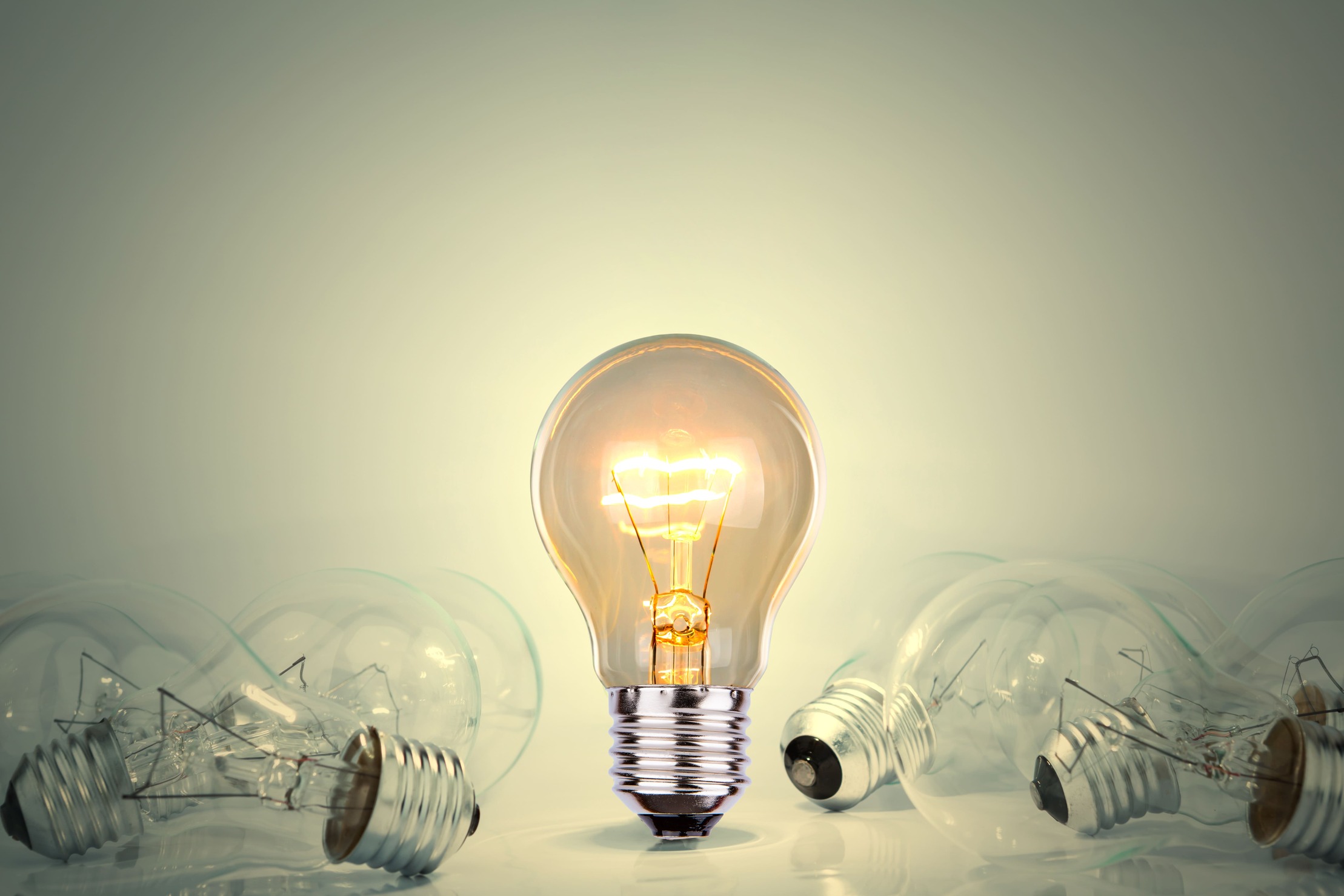
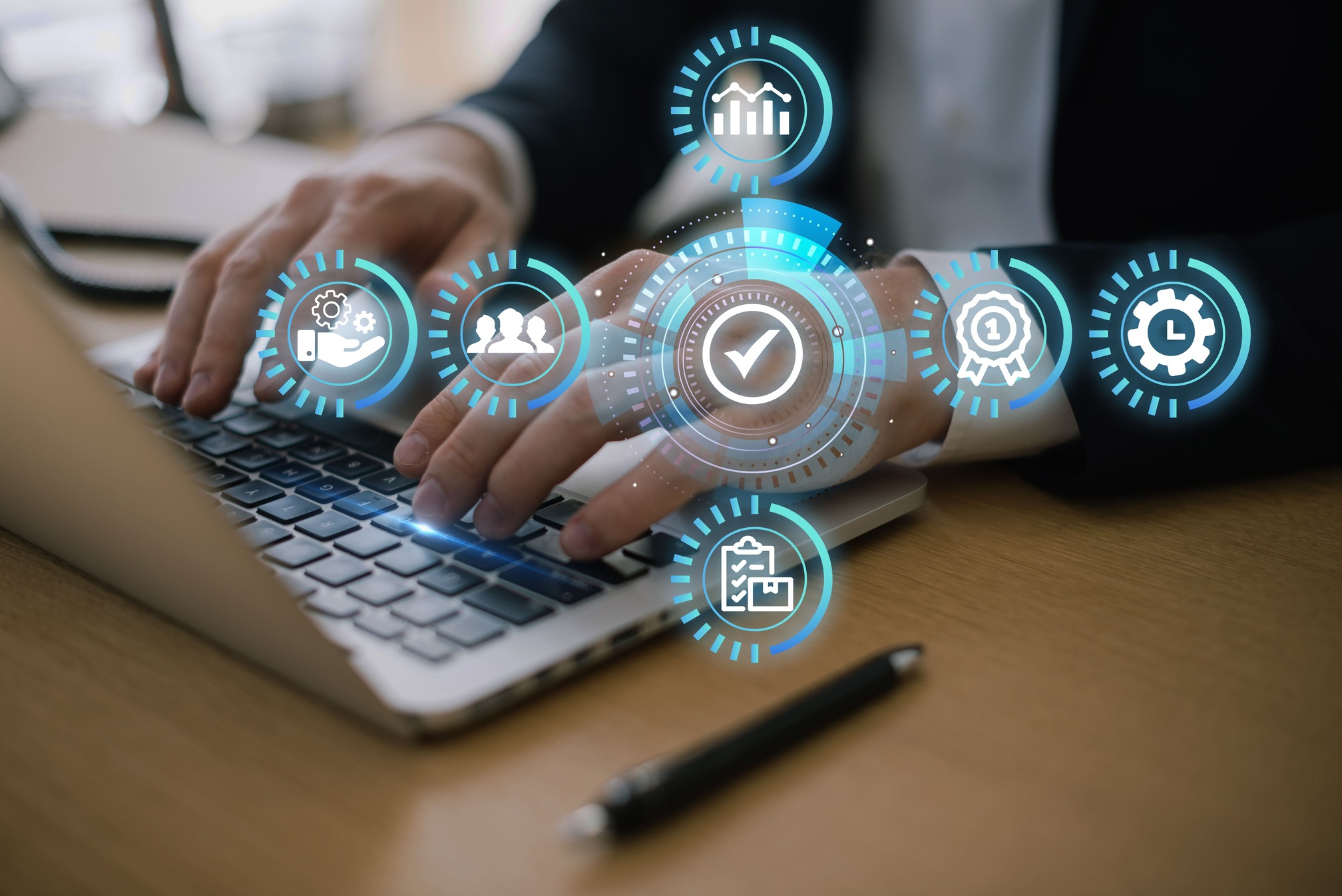
Our Solution
Our consultancy and solution (in compliance t0 ANSI/ISA 84.00.01/ IEC 61511) presents an automated mechanism to address the many issues associated with ongoing SIS Performance ownership. These features address automating the tasks associated with ongoing management of safety systems, ensure accuracy, compliance, and improve productivity by providing up-to-date knowledge of SIS status and providing notifications when problems arise. SIS performance is monitored and reported. Cost savings related to SIS testing can be significant and are easily documented.
Process Improvement Modules
- PID Control Loops
Problem Diagnosis - Upgrade To Control Loops,
MPC and Others - Digital Twin Based Control, Optimization,
Alarming and Predictive Maintenance
Problem Diagnosis
Introduction
PID (Proportional, Integral, Derivative) control loops form the cornerstone of industrial process control systems, playing a pivotal role in achieving optimal efficiency, stability, and precision in managing complex process variables. equalOT’s control loop diagnostics module meticulously examines loops dynamics and identifies loops problems such as oscillations, stiction, hysteresis, or poorly tuned controller parameters.
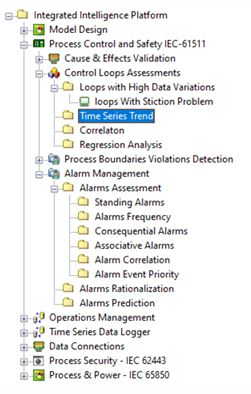
MPC and Others
Overview
Currently, advanced control engineering is seldom available at process plants. With modern control offering techniques like Model Predictive Control among others, efficiency and productivity of existing operations can increase significantly, without major hardware upgrades.
We have hardcore knowledge to model process equipment as well as design and implement advanced control algorithms. Our hybrid digital twin coupled with advanced controls have the potential to increase your productivity and offering many other benefits.
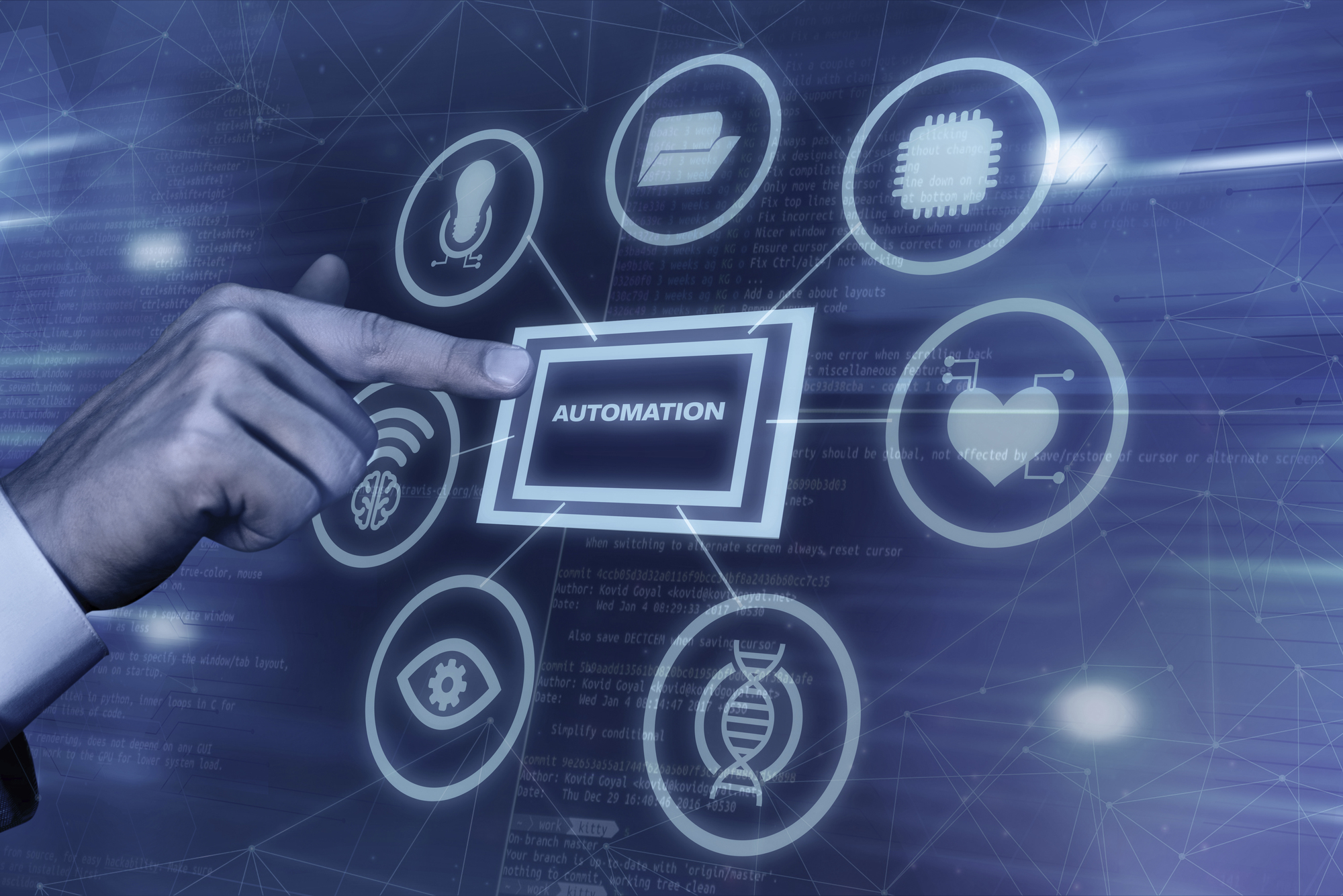
Alarming and Predictive Maintenance
Introduction
We possess unique ability to develop and deploy digital twins, starting from individual assets and moving towards full systems. Our approach generates hybrid and executable digital twins which involve high fidelity modeling and simulations (including CFD and FEA) and use of real measurement data. We can use AI techniques for generation of reduced order models for optimized controls.
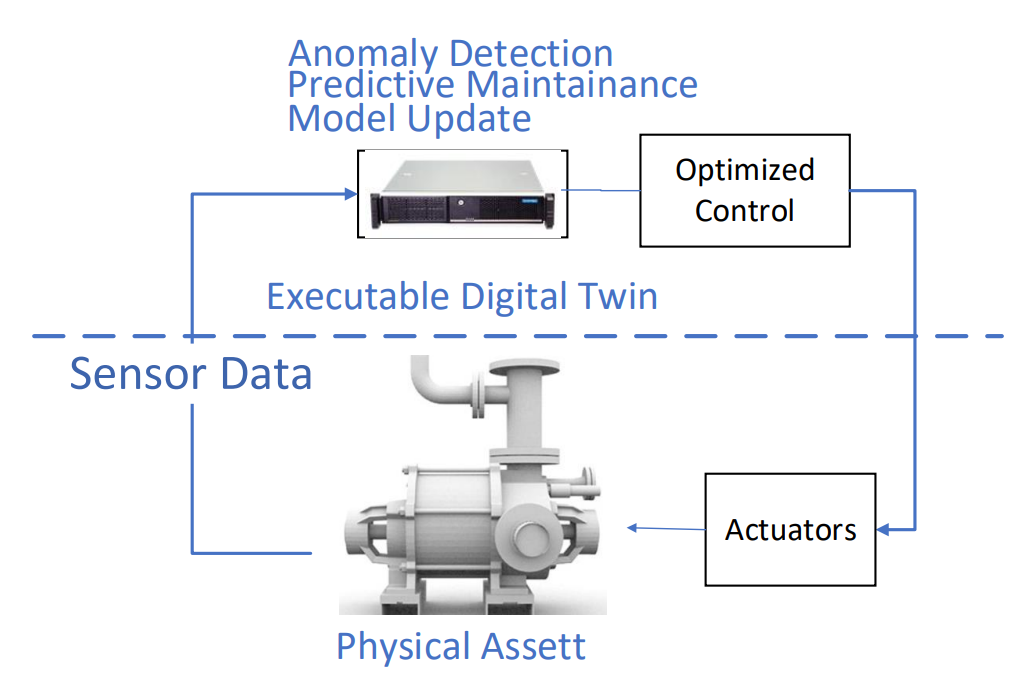
Schedule a meeting with us
If you want to learn more about us or have any queries or concerns,
do not hesitate to reach out to us.